
Dry Goods Sharing | How to Make high quality Shotcrete?
Release Time:
2021-09-15
#
The production of fiber concrete is often a headache for concrete producers-especially when it comes to shotcrete production. Usually, fiber concrete is only used for special projects. However, the production of it requires the factory to be equipped with the corresponding equipment. We present important points for producing high quality fiber concrete for shotcrete.
#
#
Design of raw materials and mixtures for fiber concrete
What do concrete plants need to consider?
Green energy technology CSM three-dimensional shear countercurrent type mineral material mixing mixer
The advantages and disadvantages of different fiber addition methods:
1. Add the fiber into the drum of the concrete mixer truck
Advantages: the use of concrete concrete mixing station mixer concrete mixing speed is very fast.
Since no fibers remain on the conveying equipment, there is no risk of fibers entering the non-fiber concrete mix.
Disadvantages: It takes a long time to add fiber and mix.
Despite the long mixing time, the concrete may still be uneven and the fibers may not be distributed evenly. As a result, clumps of fibers may occur, which may get stuck in the hose, pipe or nozzle. This metering method is not suitable for loose plastic fibers.
2. Add the fiber to the concrete mixer
Advantages: There is no risk of fibers entering the non-fiber concrete mix.
Disadvantages: It takes a long time to add fiber and mix.
① A suitable dosing device is necessary and sometimes difficult to adapt;
② The mixer area needs space for placing the batching device;
The need for longer mixing time, thereby reducing the capacity of the concrete mixing station;
Fiber clumps may still occur and may get stuck in hoses, pipes or nozzles.
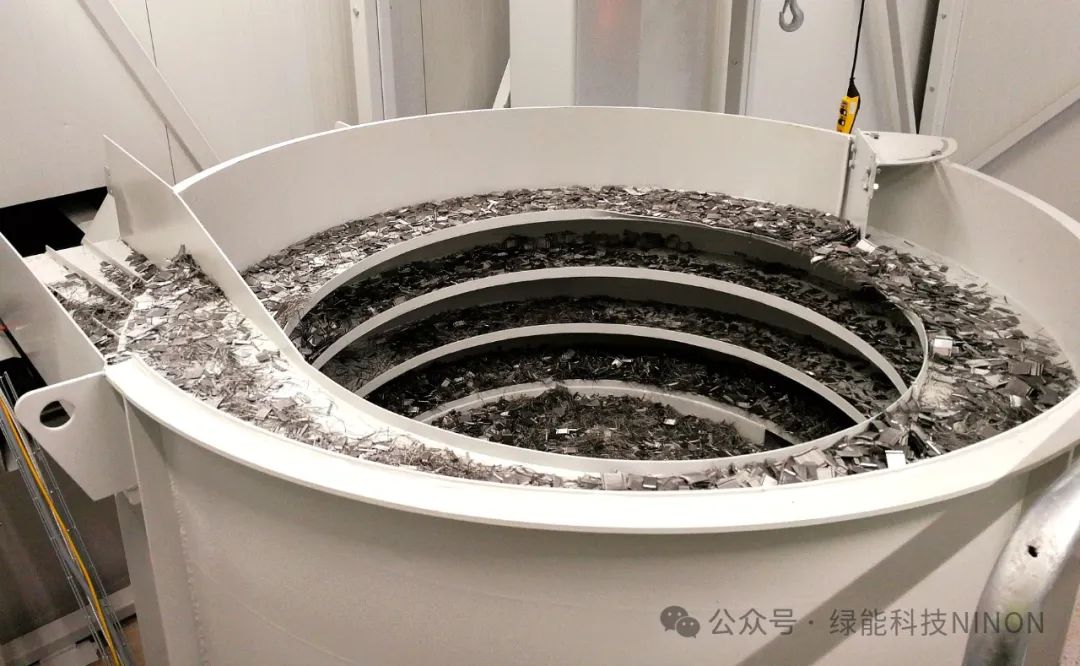
3. Add fiber at the end of the aggregate weighing belt or lifting conveyor
Advantages: It is easier to add fibers on the belt conveyor than in the concrete mixer.
Disadvantages:
① Space for batching device and conveyor is required in the unit area of aggregate warehouse;
The batching and mixing time is longer, reducing the capacity of the concrete mixing station;
③ Fiber clumps may still appear and may get stuck in hoses, pipes or nozzles.
4. Add fiber on top of aggregate flowing on weighing belt conveyor
Advantages:
① The fibers are evenly mixed; there will be no fiber lumps;
The mixing time is short, does not affect the capacity of concrete mixing station;
Applicable to all fiber types;
④ Easy to connect to aggregate box, even as a retrofit.
Disadvantages:
Some fibers may remain on the conveyor belt and may be mixed into concrete batches that are not intended for use. The production of fiber concrete, especially fiber concrete for shotcrete, requires many factors to be considered in the concrete mixing plant. It only needs high-quality materials and proper mixing design. In addition, accurate batching equipment, low batch-to-batch deviations, accurate aggregate moisture measurement and efficient mixers are all essential.
The fiber compounding method also plays a role. After all, it can significantly affect the quality of the concrete and the capacity of the plant.
Related News
undefined
Tik Tok


Fujian Green Energy Environmental Protection Technology Co., Ltd.
Service Hotline:4006655896
Tel:0595-22557155、13808548004
Email:nonnon@fjlnkj.com
Website:http://www.fjlnkj.com/
Factory Address: Hardware and Electromechanical Industrial Park, Luojiang Economic Development Zone, Quanzhou City, Fujian Province (No. 268, Luobin North Road)
Page Copyright © 2022 Fujian Green Energy Environmental Protection Technology Co., Ltd.